With A Rigorous Testing Process
- Strict raw material testing
- Quality control at all levels of the manufacturing process
- Strict corrosion resistance testing
- Strict welding quality qualification test
- Strict quality qualification test after pre-assembly of the bracket
- Strict final product inspection
Commitment to Quality Objectives
Core index: product primary qualified rate ≥99.5%, customer complaint rate ≤0.1%, failure rate in warranty period <0.05%
Certification standards: ISO 9001 Quality Management System, GB/T 35694-2017 General Technical Requirements for Photovoltaic Racking Systems, Rohs Standard, ISO14001 Standard, ISO45001 Standard, etc.
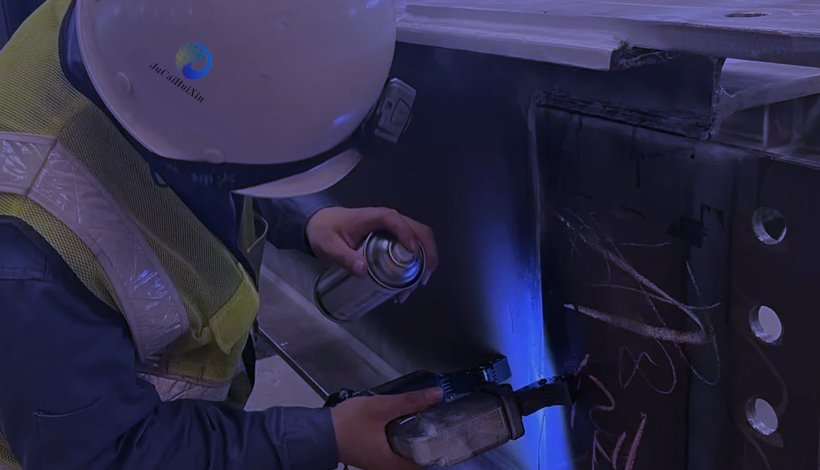
Overview Of The Quality Control Process
Every set of photovoltaic mounting bracket produced by Jucai Huixin has to go through layers of quality testing and be qualified before it can be sent to customers. Ensure that customers get 100% of the quality of photovoltaic mounts up to standard. For this reason, we have carried out quality control management from the raw materials, unqualified raw materials are absolutely not used.
The production process is also strict control, from moulding to cutting, and then to punching, our advanced production equipment can ensure that the product size of the precise standard, hole hole spacing is accurate and error-free. Proofing process is also carried out in strict accordance with the drawings, the length, width and height of the bracket are in accordance with customer standards. The thickness and uniformity of the coating should be up to standard.
PV bracket pre-installation process, if there is a problem, will also actively communicate with the customer, coordination, as soon as possible to solve the customer’s practical problems, in advance of the customer in the use of a variety of problems, to give reasonable suggestions and solutions.
After no problem in the trial installation process, mass production can be carried out, and the mass production process is still in accordance with the strict quality control process, to protect the quality of the customer’s bracket products.
After customers get our photovoltaic bracket goods, we also have free technical installation guidance, teaching customers step by step in accordance with the construction requirements for hand operation, to ensure that from piling to assembly, to the reinforcement of each screw and bolt, to the daily maintenance of photovoltaic bracket, Jucai Huixin will give nanny-level after-sales service. Ensure the user smooth installation and use.
According To Progress
At Jucai Huixin, we do these quality testing items in advance in order to ensure that the quality of our PV mounts is up to standard. The goal is to give customers peace of mind.
In Jucai Huixin factory, all steel plates, steel coils and other raw materials have to go through strict screening and product quality testing before entering the factory, the grade of steel plate, yield tensile strength, impact strength, width, thickness and length of steel plate have to be qualified before entering the factory into the warehouse.
The thickness of the galvanised layer, the amount of zinc coating, the uniformity and the appearance of the galvanised steel coils or zinc-aluminium-magnesium steel coils should be in accordance with the customer’s standards.
In Jucai Huixin, you never have to worry about the length of the PV bracket structure, we will strictly follow the customer’s requirements for accurate cutting, the cut structural material is burr-free, the cutting surface is neat and smooth, saving you the cost of cutting.
Jucai Huixin welding engineers are equipped with more than 5 years of welding, welding in the two bonded welding, argon arc welding and other welding processes, in strict accordance with the relevant process standards for standardised operation, to ensure that each weld is strong, tight, and can withstand the test of the customer.
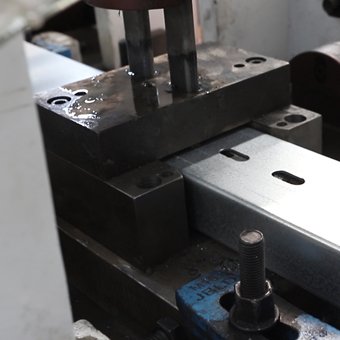
Jucai Huixin’s laser perforation machine: aperture tolerance ± 0.05mm, hole position deviation ≤ 1mm, workers strictly in accordance with the customer’s photovoltaic bracket construction drawings for the perforation operation, which indeed guarantees that the customer’s profile structure of the holes and hole spacing 100% qualified.
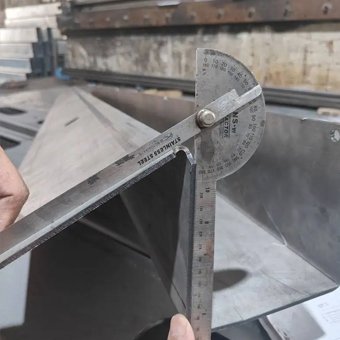
In Jucai Huixin’s factory, for customers with bending requirements, our bending machine and other equipment can also be processed for steel plate bending, to ensure that the angle is 100% in line with the customer’s photovoltaic support construction drawings. Bending machine: Angle error ≤ ± 0.5 °, R angle accuracy ± 0.3mm.
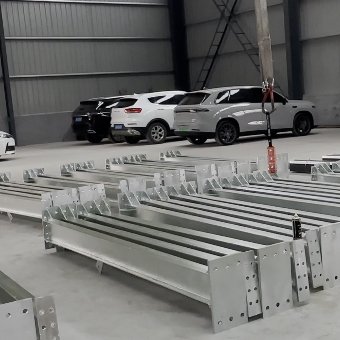
Jucai Huixin adopts a more corrosion-resistant and salt spray-resistant hot dip galvanising process, which not only increases the thickness of the zinc layer, but also forms a protective film on the surface of the bracket, making the PV bracket’s lifespan longer and its structure more durable.
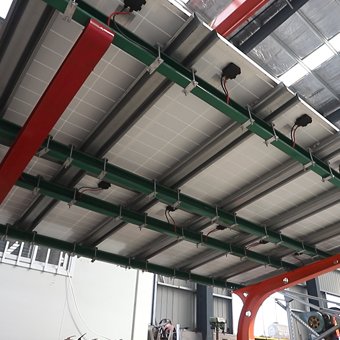
In Jucai Huixin, all the photovoltaic brackets have a sampling pre-assembly process, through the pre-installation, identify problems in advance, communicate with customers in a timely manner, and make adjustments until there is no problem in the installation process before mass production, the mass production process again in accordance with the strict implementation of the quality control process, to ensure that the bracket quality is up to standard.
Related Product
- Solar Panel Roof Mounts
Jucai Huixin produce all kinds of solar panel roof mounts.
- Balcony Solar Panel Mounts
Jucai Huixin produces a wide range of balcony solar panel mounts.
- Ballasted Ground Mount Solar Racking
Jucai Huixin produces a wide range of ballasted ground mount solar racking.
- Solar Fence
Jucai Huixin produces a wide range of solar fence.
- Single Axis Solar Tracking System
Jucai Huixin produces a wide range of single axis solar tracking system.
- Dual Axis Solar Tracking System
Jucai Huixin produces a wide range of dual axis solar tracking system.
- Solar Panel Pole Mounts
Jucai Huixin produces a wide range of solar panel pole mounts
If Have Any Problem About solar Bracket
Please do not hesitate to contact one of our account managers or technicians, who will be happy to answer any questions you may have about the photovoltaic industry.
A: The thickness of the galvanised layer should be designed according to the corrosion level of the environment:
Weak corrosive environment (e.g. urban suburbs): ≥65μm
Moderately corrosive environment ( Industrial area): ≥85μm
Strongly corrosive environment (coastal/chemical plant): ≥100μm
Testing method: Verification using magnetic thickness gauge or grid method.
Welding defects (e.g. false welding, porosity) can lead to stress concentration. Specification requirements:
Welding seam quality: no cracks in appearance, ultrasonic testing level â… qualified
Post-welding treatment : Grinding and smoothing and applying anti-corrosion layer
Key parameters: welding current, speed, interlayer temperature should be executed according to the process card.
According to GB/T 13825 standard:
Column verticality: ≤1‰
Hole position deviation: ≤±1mm
Overall flatness: ≤3mm/m
The parts that are out of order need to be repaired or scrapped.
Visual inspection: appearance of blistering, flaking, rust spots
Adhesion test: scratch method grade 0 is excellent (no peeling)
Electrochemical testing: polarisation curve method to assess corrosion rate
Full corrosion assessment at least once a year.
Static load test: apply 1.5 times the design load for 24 hours
Dynamic load test: simulate wind vibration (0.5Hz frequency, 30 minutes)
Ultimate load: 80% of the yield strength of the material
The amount of deformation should be ≤ L/250 (L is the length of the member).